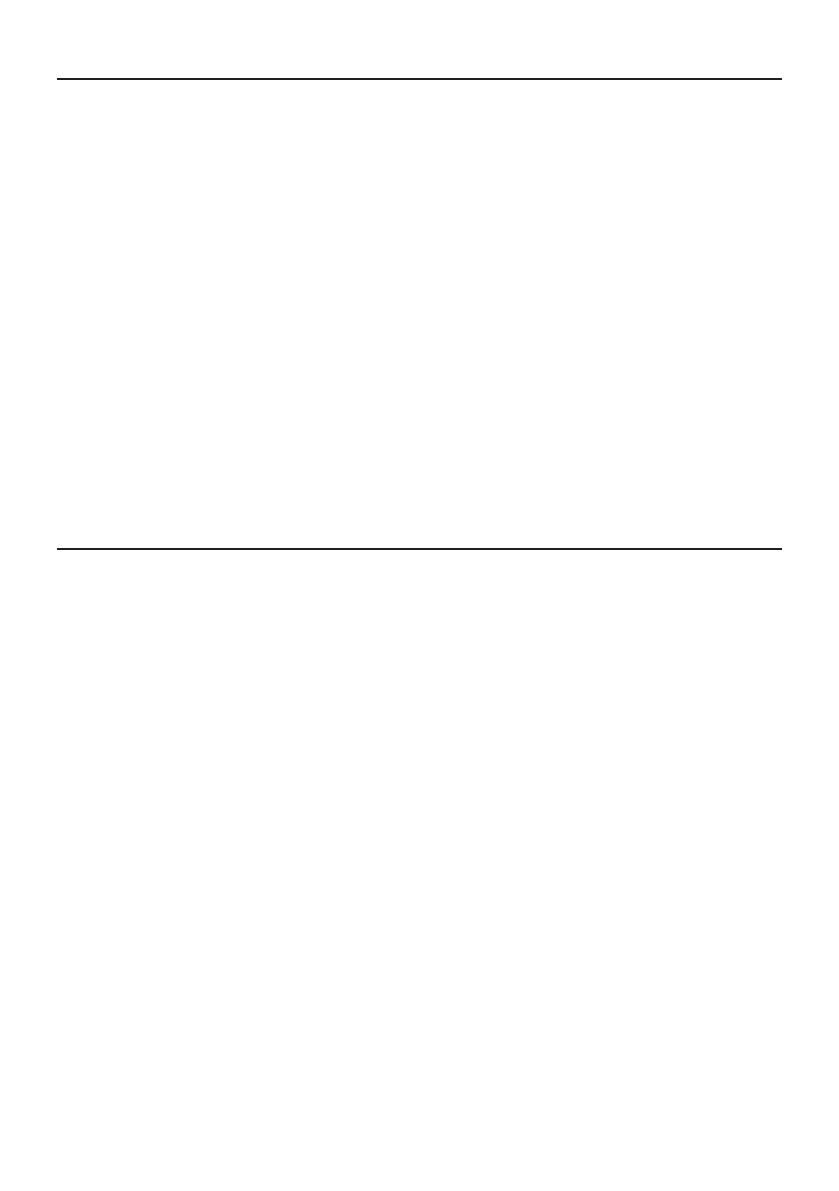
8 | nVent.com
ADDITIONAL ITEMS
Conduits (6,7)
Conduits (supplied on site) are required to
protect the
• flexible connection lead and crossover with
the rigid/flexible connection lead
• sensor connection lead.
Electrical Control Equipment
If nVent standard panels are not used, further
items will be required to complete the system:
• contactors
• circuit breakers
• residual current device (RCD) 30 mA. (Multiple
heating cable circuits up to a total length of
167 m may be protected by a single 30 mA
RCD).
• One 300 mA RCD can be used to protect up
to 1500 m EM-MI heating cable. Note, though,
that drain tracing must be protected by a 30
mA RCD in all cases.
Storage
• Storage temperature range: –40°C to +60°C
• Store all system elements in a clean, dry
place.
Equipment
• 1000 Vdc insulation resistance tester (min.
500 Vdc)
• Multimeter
PREPARING THE SUBSTRATUM
The heating cable is normally laid on firm
substratum. In the case of sloping ramps, the
substratum is backfilled and the heating cable
is laid on the reinforcement or rolled asphalt.
In suspended structures the substratum may
consist of finished slabs, prestressed concrete
or a suspended structure with poured concrete.
Steel beams or planks with a concrete surface
are also permissible.
A suspended structure is normally covered by an
asphalt layer to prevent water penetration.
The heating cable can be laid on any of these
surfaces. In the case of poured concrete, though,
it should be ensured that the surface is smooth
and all sharp objects are removed. Roadways on
a solid substratum do not require any additional
thermal insulation.
Appropriate preparations should be made for
installing the temperature and moisture sensor. If
using hot asphalt, a spacer ring or similar should
be used to protect the sensor and supply lead
from the high asphalt temperature, as otherwise
the electronic components may be destroyed.
The remaining space can then be filled once it
has cooled. Please note that to ensure long-term
stability, any exposure of the sensor and supply
lead to an exposure temperature of up to 80°C
must be kept as brief as possible. For further
details, please refer to the operating instructions
for the sensor.