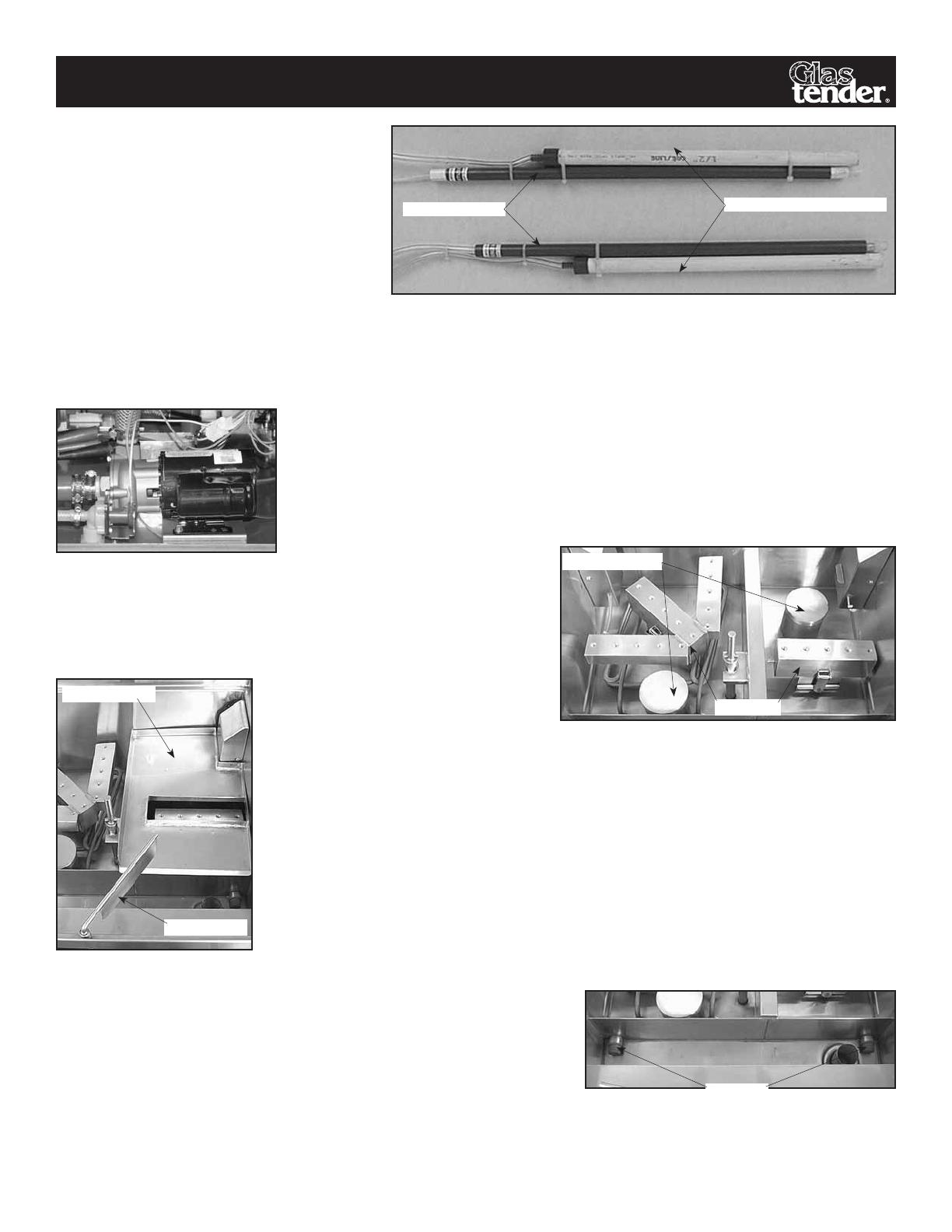
Glastender, Inc. • 5400 North Michigan Road • Saginaw, MI • 48604-9780
800.748.0423 • 989.752.4275 • Fax 989.752.4444 • www.glastender.com
13
The chemical pumps have chemical feed lines
that are attached to a chemical low-level sensor
pick-up tube. One set of lines is labeled for
detergent and the other for sanitizer. Both set
of lines must be placed inside the appropriate
chemical container. The purpose of the chemi-
cal low-level sensor pick-up tube is to make the
low-level chemical light flash when the chemi-
cals get low. There is an air pressure switch on
the other end of the chemical low-level pick-up
tube line and when the chemical level gets low the pressure on the switch decreases, turning the switch on, and causing the
low-level chemical light on the switch panel to blink. It is very important to clean the pick-up tube assembly from time to
time and to prevent the assembly from being cracked or damaged. Debris clogged in the pick-up tube or a crack or hole
in the pick-up tube assembly can cause a false low level chemical reading.
When the fill switch is on, turning on the conveyor switch puts the conveyor in motion.
Whenever the conveyor is in motion, water is spraying through the spray boxes in each
of the tanks. There is a water recirculating pump for each tank that sucks water from the
tank and forces it through the spray box and onto the glassware. It is important to have
the pump inlet screens in place to prevent foreign debris (broken glass, lemon seeds, etc.)
from being sucked in and damaging
the water recirculating pump.
Glassware is placed on the rotating conveyor so it can pass through
the wash section and then the rinse and sanitize section. The GT-24
and GT-30 glasswashers have a glass stop arm (or flag) that stops the
conveyor when the glassware strikes it. This is intended to prevent the
machine from operating constantly and
washing the same glassware repeatedly.
However, during busy times, the glass
stop arm can be manually moved to the
side so the conveyor will run constantly.
The GT-24 and GT-30 also have three curtains and a rinse tank guide. The front curtain is
to prevent water from splashing out the front of the machine. The wash and rinse curtains
run perpendicular to the front curtain and are intended to prevent the wash and rinse water
from mixing. The rinse tank guide is a stainless cover over the rinse tank (it has a hole over
the spray box) that guides the used rinse water to the drain compartment so the rinse water
is not used more than once. Wash water is re-used, but the constant splashing causes much
of the water to escape into the drain tank, so fresh water and chemicals are being regularly
added to both the wash and rinse tanks. Since the rinse water is not re-used, the rinse tank
uses more water than the wash tank when the machine is in operation.
At the end of each day of operation, turn off the conveyor and fill switches
and remove the drain plugs to empty the wash and rinse tanks. [NOTE:
Always be careful when removing the drain plugs, since the wash water
is hot.] Simple daily cleaning takes approximately five minutes. Follow
the cleaning procedures outlined on pages 17 and 18 of this manual and
perform the heavier cleaning procedures, such as de-liming, as necessary.
how the Glasswasher operates (contInued)
Detergent and Sanitizer Feed Lines with Chemical Low Level Sensor Pick-Up Tubes Attached
Chemical Feed Line
Low-Level Sensor Pick-Up Tube
Water Recirculating Pump
Pump Inlet Screens
Spray Boxes
Inside view of wash and rinse tanks for clockwise GT-24
Rinse Tank Guide
Glass Stop Arm
Drain Plugs