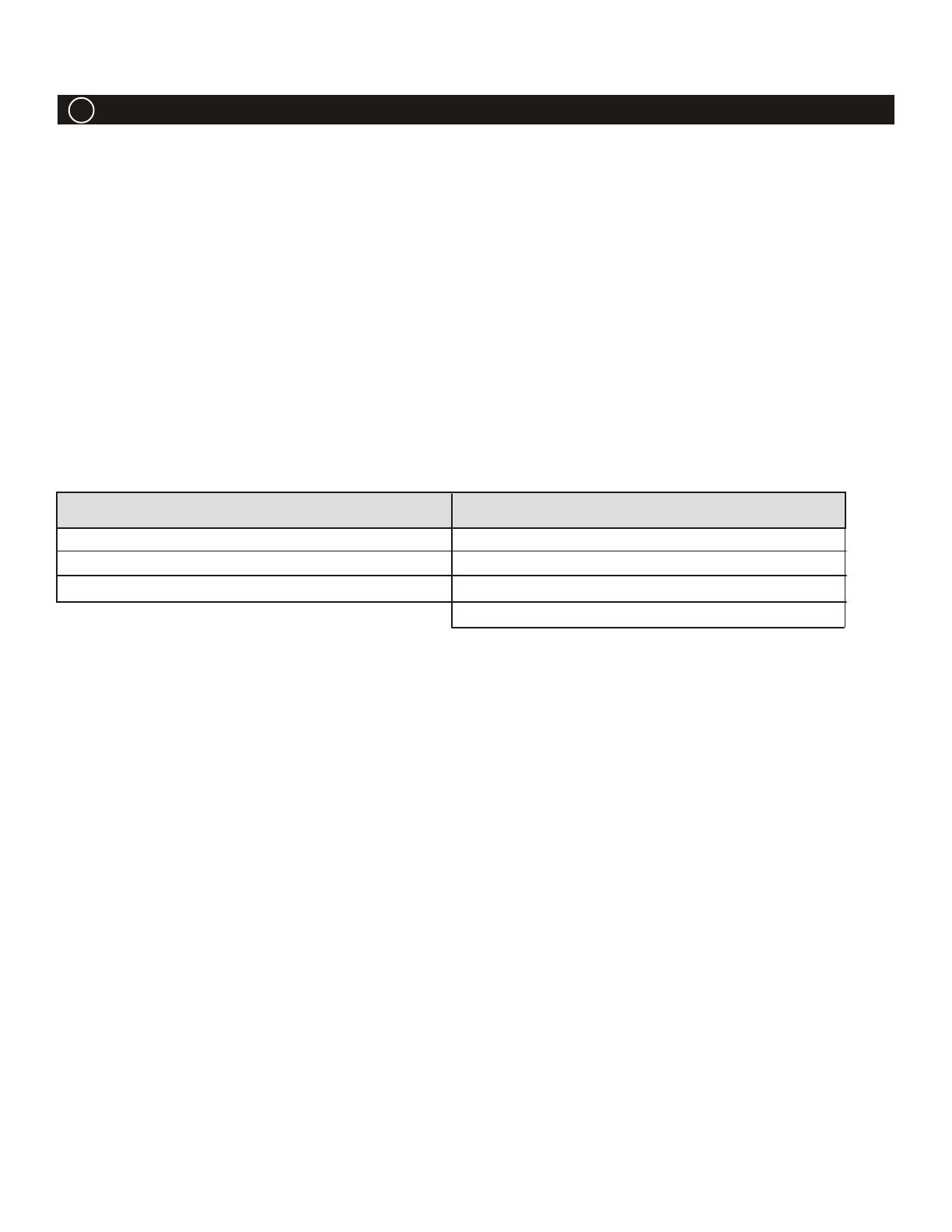
Power Center Operation:
The Power Center PCB is the true brain of the system. The micro-controller on the PCB is constantly sending
signals through the communication wires to the Controller and polling the system to determine which circuits should
be on and which should be off. When an equipment button, such as Auxiliary 1, is pressed, impulses are sent via
the communication wires (yellow and black) between Power Center micro-controller and the Indoor Controller
micro-controller. If all impulses received at the Power Center micro-controller are consistent, the system then looks
at the DIP Switch settings to determine if an option for this circuit has been set. If the DIP Switch settings do not
indicate a delay is needed, signals are sent back to the Controller to turn on the appropriate LED and display the
ON message. At the same time, a signal is sent to one of the two Driver Chips on the Power Center PCB.
The Driver Chips can be thought of as a series of small relays. When one of the Driver Chips receives a signal,
it closes a contact which passes 24 VDC to the appropriate relay coil socket, in this case AUX 1. Each relay driver
chip activates a specific set of relay coil sockets (see the chart below). If a Driver Chip fails, it is usually caused by
either shorted relay coil wires, a shorted relay coil, or a relay not designed for the 24 VDC coil voltage (i.e., 24 VAC
rather than 24 VDC).
The Reset button, located in the upper left hand corner of the Power Center Bezel, when pressed, resets the
Power Center micro-controller and changes time and date to the default settings (i.e., 1:00 P.M. 01/31/96 WED).
Pressing this button will not remove any programming, AUX labels, etc.
Memory:
All programming, labeling, temperature settings, etc., are stored within a EEPROM (Electronically Eraseable
Programmable Read Only Memory) chip. This chip is located on the PCB and will retain all settings indefinitely,
even if power is lost for an extended period. To remove information from the system, either press the Cancel button
to remove individual items, or the Clear Memory item from the Menu, to reset all items to their default settings. The
battery attached to the PCB is only needed to keep the clock running during a power outage, so when power is
restored, time and date will be correct.
Specifications:
Supply Voltage: 24 VAC (from secondary of transformer)
Operating Voltage: 5 VDC
Circuit Activation: Serial Communication
Time / Date backup: Supplied by 9 Volt battery at Power Center
Memory backup: EEPROM on Power Center PCB
Driver Chip in U9 socket activates: Driver Chip in U10 socket activates:
Relay Socket for Filter Pump
Relay Socket for Auxiliaries 1 throu
h 7
Relay Socket for Spare Auxiliary
Relay Socket for Electric Heater
Solar Booster Pump Socket
All JVA Relay Coils
Low Volta
e Heater Relay Coil
AquaLink
®
RS Troubleshooting
2 Power Center
3