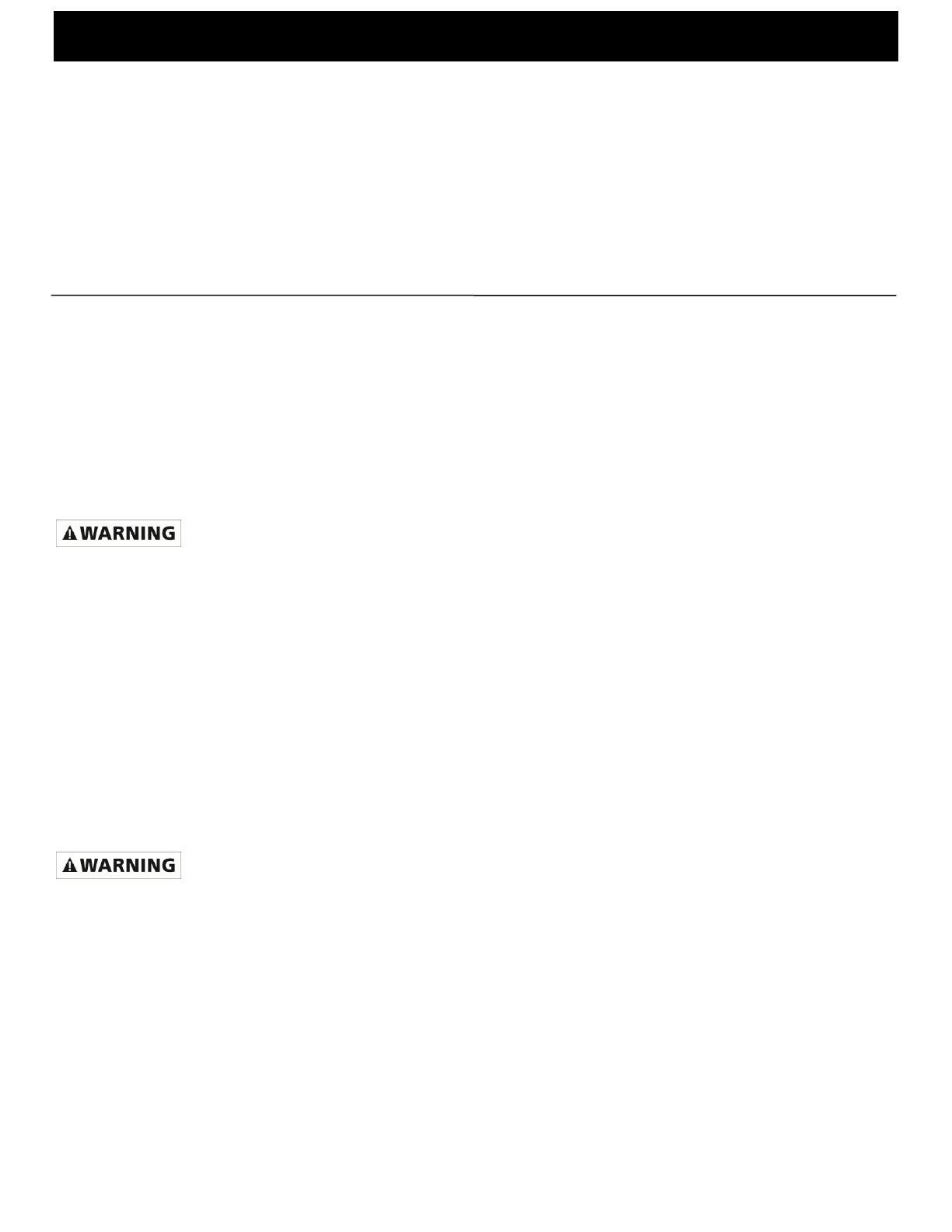
Specifications Information and Repair Parts Manual 5760-95 thru 576E-95
Please read and save this Repair Parts Manual. Read this manual and the General Operating Instructions carefully before attempting to assemble,
install, operate or maintain the product described. Protect yourself and others by observing all safety information. The Safety Instructions are contained
in the General Operating Instructions. Failure to comply with the safety instructions accompanying this product could result in personal injury and/or
property damage! Retain instructions for future reference. AMT reserves the right to discontinue any model or change specifications at any time without
incurring any obligation.
©2011 American Machine & Tool Co., Inc. of PA, A Subsidiary of The Gorman-Rupp Company, All Rights Reserved.
Periodic maintenance and inspection is required on all pumps to insure proper operation. Unit must be clear of debris and sediment. Inspect for leaks and loose bolts. Failure
to do so voids warranty.
Submersible Shredder Pumps
Refer to pump manual 1808-636-00 for General Operating and Safety Instructions.
DESCRIPTION
These heavy duty centrifugal Submersible Shredder Pumps are intended for use in residential, commercial, and industrial settings. Examples include:
Sewage, wastewater, and other general processing applications involving dirty liquids with small solids (see size chart below). Submersible design
means low noise and no priming issues.
Each unit is completely assembled and includes a self-cleaning, semi-open cast iron impeller featuring a tungsten carbide cutting tip for durability while
helping to break-up solids. Pumps incorporate a mechanical shaft seal with long-lasting silicon carbide wear faces and feature a secondary shaft seal
and oil chamber.
Pumps have a 3450 RPM electric motor fitted with an unfinished power cord that requires field wiring (no controls are supplied). Motors are rated
continuous duty and single phase units have automatic restart thermal overload protection. Handle liquids from 40° to 104° F (4° to 40° C). For use with
non-flammable liquids compatible with pump component materials.
MAINTENANCE
Make certain that unit is disconnected from power source before
attempting to service or remove any components!
POWER CORD REPLACEMENT
Periodically inspect power cord and replace whenever abrasion,
cracking, softening, or other signs of deterioration are found.
Refer to Figures 1 and 2.
1. Place unit on workbench in upright position. Clean dirt and
rust from around wire cover (Ref. No. 7).
2. Remove two fasteners (Ref. No. 4) which hold cord retainer
(Ref. No. 3).
3. Remove fastener(s) (Ref. No. 5) at handle (Ref. No. 6) to
free wire loom (Ref. No. 2).
4. Remove four fasteners (Ref. No. 8) which hold wire cover in
place.
5. Carefully pry cover from unit with screwdriver.
IMPORTANT: Be careful to keep rust and other debris from falling into
motor housing during cover removal.
6. Take note of proper wire configuration, and connect new
power cord (Ref. No. 1) in identical fashion.
If unsure about above information or wiring diagrams, consult an
electrician familiar with motor wiring.
7. Clean sealing flanges if necessary and reassemble pump in
reverse order.
IMPELLER INSPECTION /REPLACEMENT
If pump develops poor performance characteristics, impeller may be
worn or clogged.
IMPELLER INSPECTION
Refer to Figure 2
1. Place unit on workbench in upright position and clean rust
and buildup from around pump-to-motor flange.
2. Remove four short fasteners (Ref. No. 15) which attach
pump to motor.
3. Lift motor assembly up out of pump assembly and lay on
workbench in horizontal position. Rap down on pump body
with soft mallet if necessary to separate parts.
4. Inspect impeller (Ref. No. 26). If clog is found, remove
debris and reassemble in reverse order. If damage to
impeller is found, such as pitting, deep grooves, or
breakage, proceed to next section.
IMPELLER REPLACEMENT
1. Remove impeller fastener (Ref. No. 28) by unscrewing in
counterclockwise direction.
NOTE: To prevent motor shaft from turning, wedge a screwdriver
between impeller vane and impeller fastener (see Figure 2).
2. Slide off impeller washer (Ref. No. 27). Impeller is keyed to
motor shaft and can now be pulled free.
3. Install replacement impeller and reassemble in reverse
order.
MECHANICAL SEAL REPLACEMENT
Motor internals are protected from contact with liquid being pumped by
a mechanical shaft seal and oil cavity. When seal wears out, potential
motor life will be compromised. Therefore, periodic seal replacement is
recommended. Time interval between replacements will depend on
abrasiveness of liquid being pumped, temperature, total accumulated
runtime, etc.
IMPORTANT: Always replace seal head (Ref. No. 18) and both seal
seats (Ref. Nos. 17 & 19) at same time to insure proper mating of
components.
Refer to Figure 2
1. Disassemble pump by following directions in both “Power
Cord Replacement” and “Impeller Inspection / Replacement”
sections.
2. With unit on its side and wire cover, pump assembly, and
impeller removed, lift shaft key (Ref. No. 13) from shaft/rotor
(Ref. No. 12) using a pliers.
3. Clean rust and buildup from unit.
4. From top of unit, remove four long fasteners (Ref. No. 10)
which attach lower end bell (Ref. No. 16) to motor case (Ref.
No. 11).
5. Rap on ears of lower end bell with a soft mallet to break it
free from motor case. Then carefully guide lower end bell
along with shaft/rotor and bearing assembly out of motor
case.